Premier four verrier électrique
L’électrification des procédés est souvent la clé pour décarboner l’industrie. C’est le cas ici avec la construction du premier four verrier électrique de cette taille au sein de l’usine Verallia de Cognac.
Le four, qui produira du verre blanc à destination des consommateurs de Cognac, a une capacité de 180 tonnes par jour. Les premières livraisons sont attendues pour la fin du 2e trimestre 2024, a indiqué Verallia dans un communiqué en marge de ses résultats du premier trimestre 2024.
Selon son rapport RSE, le groupe vise une réduction de ses émissions de CO2 de 46% en 2030 par rapport à 2019 (en valeur absolue, sur les scopes 1 et 2, c’est-à-dire les émissions de ses propres opérations).
Cet objectif, validé par l’organisme SBTi (Science Based Targets initiative), s’articule autour de trois axes principaux : le déploiement de fours 100% électriques ou hybrides (80% électricité et 20% gaz), le développement du recyclage du verre avec notamment l’augmentation du taux de calcin intégré dans les fours et, enfin, l’utilisation croissante d’énergies renouvelables et bas-carbone.
Digitalisation de la ligne de production
Profitant de la création de ce nouveau four et de la modernisation de l’ensemble de la chaîne de production, les équipes de Verallia Cognac ont confié à OperaMetrix la digitalisation de la chaîne de production via notre solution spécialisée d’affichage dynamique.
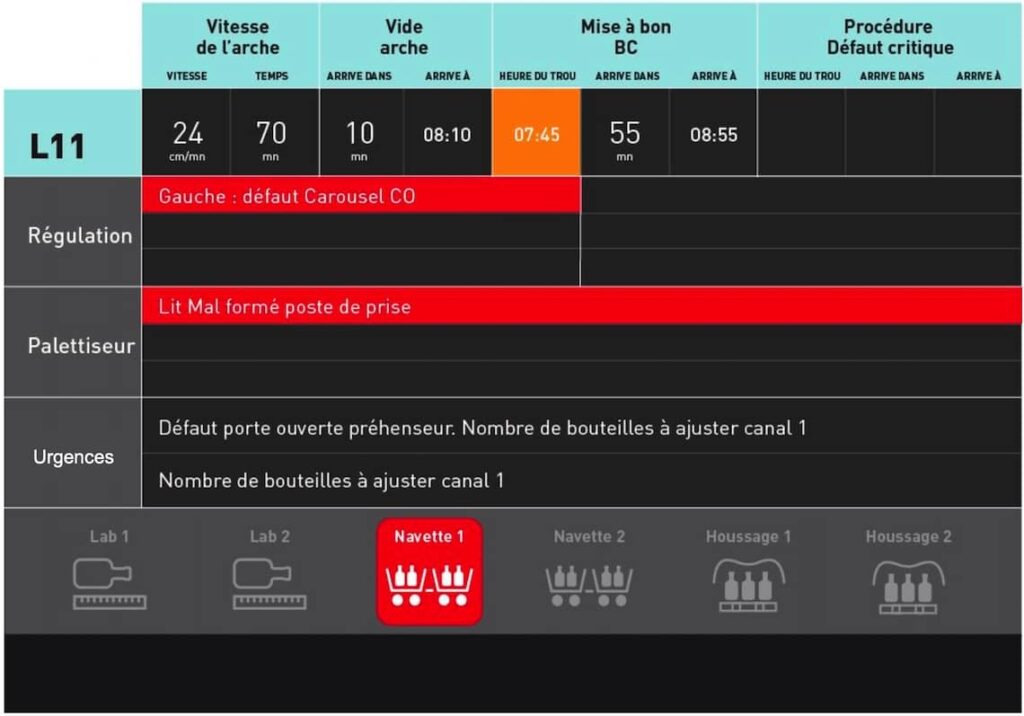
Notre solution permet de visualiser l’ensemble des systèmes et des défauts présents sur la ligne de production afin de réagir rapidement lors d’une défaillance permettant de limiter les pertes de production.
Lorsqu’une défaillance est détectée sur une ligne de production de bouteilles, l’ensemble de la production impactée est détruite et retourne dans le four pour être soufflée à nouveau.
Réagir plus rapidement lors d’une défaillance, c’est limiter au maximum les pertes de production et donc d’améliorer la productivité tout en réduisant le bilan carbone.
Affichage moderne et ergonomique
Plusieurs systèmes d’affichage sont disposés le long de la chaîne de production afin de s’adapter aux différents usages :
- Écrans dynamiques professionnels 65 pouces connectés le long de la chaîne de production pour une vision à longue distance.
- Écrans ergonomiques dans les cabines de pilotage de la ligne de production.
- Écrans de synthèse dans les bureaux et les salles de pause.
Il est également possible de déployer notre solution sur tablette et smartphone suivant les besoins.
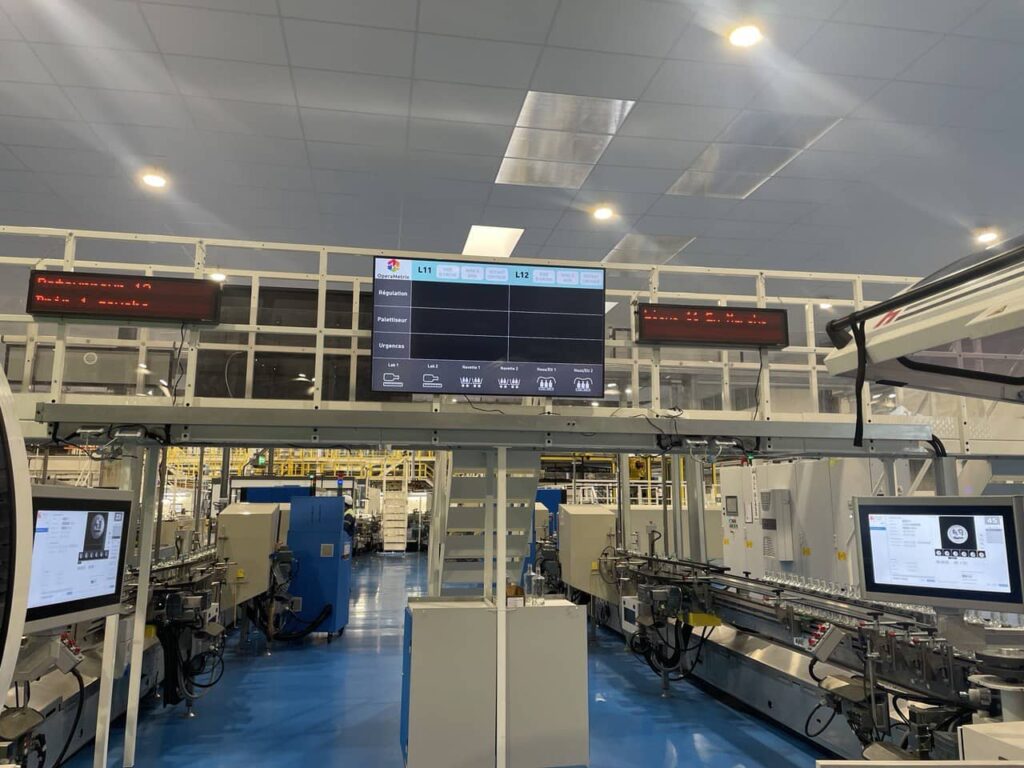
Focus sur l’affichage dynamique usine
Issu du Lean Management, il est utilisé dans les environnements industriels pour présenter des informations opérationnelles en temps réel. Il peut inclure des tableaux de bord interactifs, des graphiques, des indicateurs de performance clés (KPI), des alertes, des vues issues de caméras de surveillance, des messages, etc. Ils sont affichés sur des écrans situés dans des zones stratégiques de l’usine ou d’un atelier de production.
Quels bénéfices en retirer ?
- Amélioration de la communication : Facilite les échanges entre équipes.
- Optimisation des décisions : Aide à identifier les écarts pour agir rapidement et optimiser les processus.
- Détection rapide des problèmes : Permets d’identifier les anomalies et pannes pour minimiser les interruptions.
- Suivi des performances : Offre un suivi en temps réel des objectifs et indicateurs, améliorant l’efficacité.
- Engagement des employés : Motive les équipes en valorisant leurs contributions et en fournissant des informations transparentes.
Nous remercions toutes les équipes de Verallia France pour leur confiance dans la réalisation de ce projet ! Nous sommes fiers de vous accompagner et avons hâte de poursuivre cette belle collaboration au service de la performance de nos industries.